
Recycling the 'Unrecyclable': A New Class of Thermoset Plastics (Op-Ed)
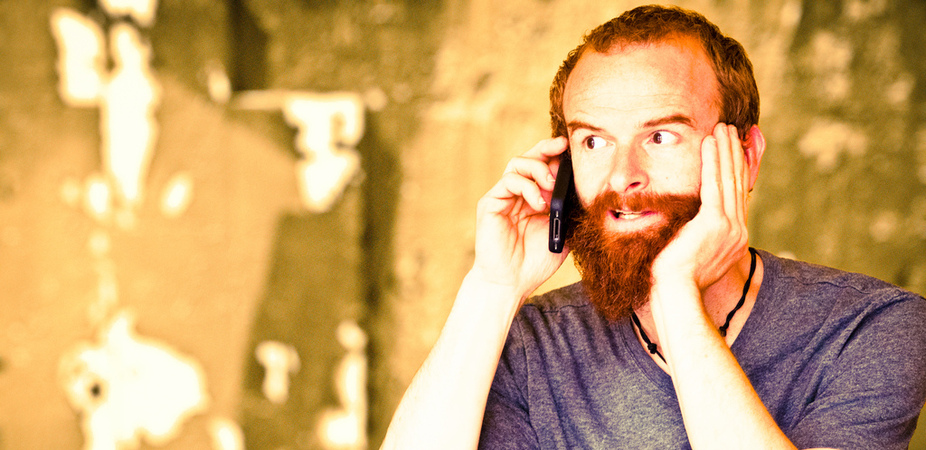
This article was originally published at The Conversation. The publication contributed the article to Live Science's Expert Voices: Op-Ed & Insights.
Plastics comprise around 10% of solid waste in Australia. And while we can recycle certain types, there is a group of particularly stable plastics called thermosets, common in electronic devices, which can’t be broken down and recycled – until now.
In a paper published in Science today, researchers describe a way to manufacture recyclable thermosets, thus allowing the plastics to be broken down and reformed.
So what is a thermoset, and what makes it so difficult to recycle? First, let’s examine the properties of traditionally recyclable plastics – thermoplastics – and compare them to thermosets.
Thermoplastics – such as plastic milk bottles, Lego bricks and guitar picks – can be melted and reshaped repeatedly. If you hold a flame to a plastic milk bottle, it will warp and melt (although I recommend against doing so as the fumes aren’t very good for you).
But thermosets – found in kitchen utensils (think of a plastic spatula) and in electronic components such as circuit boards – retain their strength and shape even when heated, making them ideal for the production of permanent components with large, solid shapes.
This ability to withstand heat is due to the “curing” step in manufacturing – such as heating, pressure and adding catalysts – which changes the state of the material at the molecular level.
As a result of curing, molecular chains in a thermoset are chemically bonded into exceptionally strong cross-linked networks. These prevent a thermoset object from melting as a thermoplastic would; when thermosets are heated, they crack or become charred.
Most common types of thermosets include epoxies, phenolics, polyesters and silicones. In general, thermosets are known for their good adhesion, high chemical and heat resistance and excellent mechanical and electrical insulating properties.
Because of these superior properties, thermosets are used in a broad range of applications in the microelectronics, transportation and aerospace industries, as well as in varnishes and glues.
Thermosets resist heat much better than thermoplastics.
Breaking down the unbreakable
The authors of today’s Science paper created recyclable thermosets called poly(hexahydrotriazine)s (PHTs) which break down in strong acid. The pure monomers (single small molecules of the plastic material) were recovered and reused (polymerised) to make new products.
The properties of PHTs were similar to those of the traditional, unrecyclable thermosets: rigid, heat-resistant and chemically stable and displaying excellent resistance to solvents and environmental stress, especially when reinforced with carbon nanotubes.
Moreover, by varying the combinations and compositions of the monomers used in their reactions, the researchers were able to produce elastic gels with self-healing properties. These gels can also be broken down in strong acid.
This work is an important advance as thermosets have long been considered impossible to recycle.
Depending on the manufacturing process, substances can yield both thermoset and thermoplastic products:
- paraformaldehyde is commonly used for manufacturing of thermosets such as phenolics, and thermoplastic polyoxymethylene (POM). POM is used in precision parts and high performance engineering components such as small gear wheels and ball bearings
- aromatic and aliphatic amines are used for production of thermoset benzoxazine resins, which are then used for manufacturing products such as high-temperature composites and electronic components. These amines are also raw materials used for producing thermoplastics including aromatic nylons for manufacturing high–strength Kevlar fibres (such as those found in some bullet-proof vests).
Simply using different combinations of monomers provides an extremely versatile materials platform. The polymerisation process reported in Science today is based on the well-understood reaction of amines with paraformaldehyde to prepare a new class of thermosets.
This method can be easily used on a wider scale with the existing facility and equipment in the resin industry. It is both technically feasible and inexpensive to produce these recyclable thermosets at the commercial scale.
These novel thermosets would replace existing thermosets in many applications such as in modern electronic devices, as well as applications in the automotive and aerospace industries.
But most importantly, the majority of products made with traditional thermosets go to landfill. If this research is implemented widely, we’ll see fewer thermosets in landfill and more being recycled, just like thermoplastics.
Qipeng Guo receives funding from the Australian Research Council through its Discovery Projects and from The Advanced Manufacturing CRC in partnership with The Victorian Centre for Advanced Materials Manufacturing and VR TEK Global Pty Ltd.
This article was originally published on The Conversation. Read the original article. Follow all of the Expert Voices issues and debates — and become part of the discussion — on Facebook, Twitter and Google +. The views expressed are those of the author and do not necessarily reflect the views of the publisher. This version of the article was originally published on Live Science.
Sign up for the Live Science daily newsletter now
Get the world’s most fascinating discoveries delivered straight to your inbox.