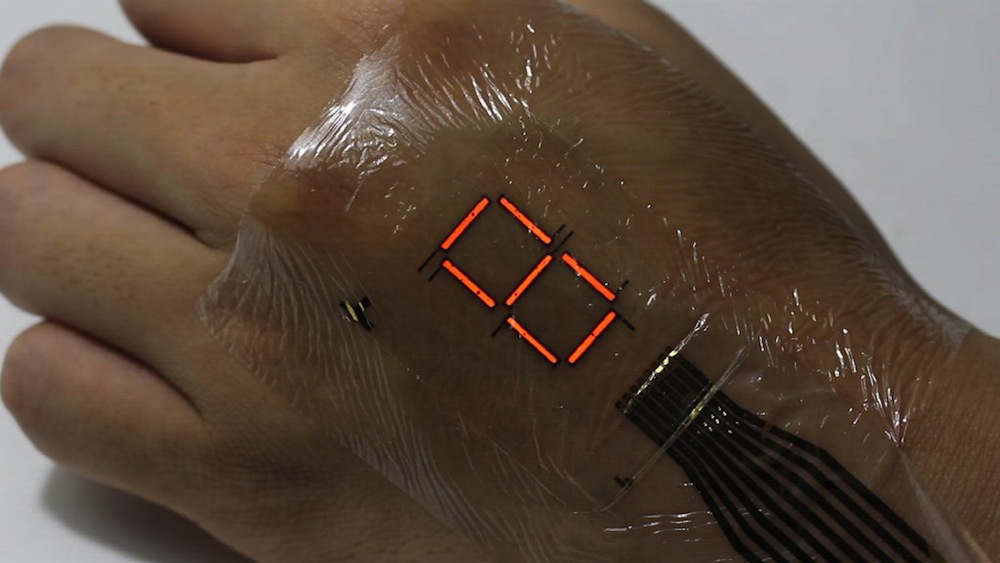
Your smartphone could one day be replaced by an electronic display laminated to the back of your hand, if the inventors of a new ultrathin "e-skin" have their way.
For the first time, Japanese scientists have demonstrated a superflexible electronic skin (or e-skin) display, made from organic electronics, that doesn't degrade when exposed to air. And crucially, the researchers used processes similar to the way organic light-emitting diode (OLED) displays are manufactured for conventional smartphones and TVs.
Organic electronics, made from carbon-based polymers, hold huge promise for wearable devices because they are far lighter and more flexible than traditional electronics made from inorganic materials, such as silicon and gold. But OLEDs and organic light detectors normally degrade in air, so they typically need bulky protective coatings that decrease their flexibility. [Body Bioelectronics: 5 Technologies that Could Flex with You]
Now, a team from the University of Tokyo has developed a unique method to create a protective coating that can shield the electronic components from the air while remaining thin enough to stay flexible.
"Our e-skin can be directly laminated on the surface of the skin, allowing us to electronically functionalize human skin," said Takao Someya, a professor in the Department of Electrical and Electronic Engineering at the University of Tokyo, and author of a paper on the new device published April 15 in the journal Science Advances.
"We think that functionalizing the skin may replace the smartphone in the future," Someya told Live Science. "When you carry an iPhone, it is a bulky device. But if you functionalize your own skin, you don’t need to carry anything, and it's easy to receive information anywhere, anytime."
Previous organic electronic displays have been built using glass or plastic base materials, or substrates, but their flexibility was limited by their thickness. Other, thinner versions have been manufactured, however, these materials have not been stable enough to endure in air for more than a few hours.
Sign up for the Live Science daily newsletter now
Get the world’s most fascinating discoveries delivered straight to your inbox.
Someya's group was able to extend the device lifetime to several days by creating a protective film, called a passivation layer, which consists of alternating layers of inorganic silicon oxynitride and organic parylene. The film shields the device from damaging oxygen and water vapor but is so thin that the entire device is just 3 micrometers (millionths of a meter) thick and highly flexible, the researchers said. For comparison, a strand of hair is about 40 micrometers thick.
Substrates this thin can be easily deformed by the high-energy processes needed to produce the ultrathin, transparent electrodes that connect the components, Someya said. So, the group's second innovation was to optimize these processes to reduce the required energy to a level that did not damage the ultrathin materials.
In the near future, this technology could be used to monitor people's health, Someya said. To demonstrate its potential, his team created a device consisting of red and green OLEDs and a light detector that could monitor the concentration of oxygen in a human subject's blood when the e-skin is laminated to the person's finger using highly flexible adhesive tape. [Bionic Humans: Top 10 Technologies]
The scientists also created both digital and analog displays that could be laminated to the skin, and all of the devices were flexible enough to distort and crumple in response to body movement, without losing their functionality.
"The potential uses range from information display to optical characterization of the skin," said John Rogers, a professor of materials science and engineering at the University of Illinois, who also works on developing e-skin but was not involved with the new study. "Opportunities for future research in this context include the development of power supply systems and of wireless schemes for data communication and control."
By employing materials and processes that are already used in the industrial production of OLED displays, Someya said the group's work should be able to transition smoothly to large-scale production.
Hyunhyub Ko, an associate professor of chemical engineering at the Ulsan National Institute of Science and Technology in South Korea who also researches e-skin, agrees that this method could eventually be applied to the manufacturing of commercial products.
"The formation of [an] ultrathin and flexible passivation layer is a challenging task," Ko told Live Science. "Their fabrication process includes the solution coating and chemical vapor deposition methods, and thus can be scaled up for commercial products."
Follow Live Science @livescience, Facebook & Google+. Original article on Live Science.
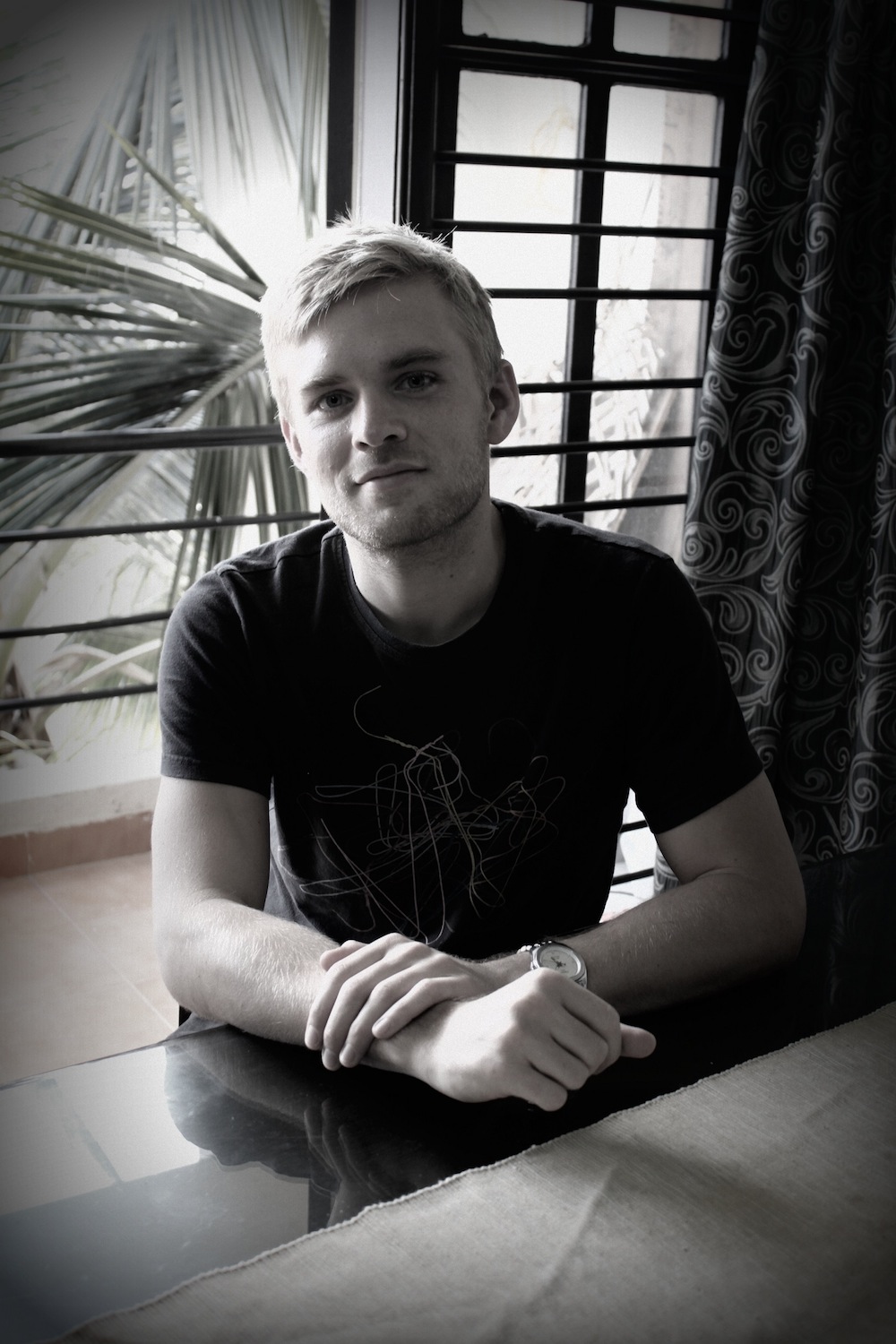