Hair on Demand: Researchers Create 3D-Printed Fur
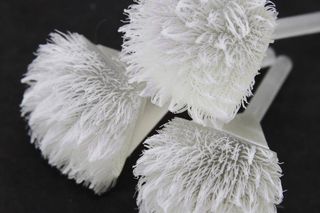
3D printers aren't just for making small, rigid, plastic models — now, these figurines can have long, flowing, 3D-printed locks.
Researchers have developed software and a new technique for creating 3D-printed hair, or hair-like structures, which can be used in a wide array of forms and functions. Beyond the aesthetic appeal of individual hairs, the 3D-printed version could be designed for connecting, moving or even sensing other objects.
"Although it is the same material, you can vary its stiffness from something like a toothbrush bristle to synthetic hair or fur," said study lead author Jifei Ou, a graduate student in the Tangible Media Group at the Massachusetts Institute of Technology. The project, dubbed Cilllia, was presented in May at the Association for Computing Machinery’s CHI Conference on Human Factors in Computing Systems. [The 10 Weirdest Things Created by 3D Printing]
"The goal of Cilllia is not to replicate hair, but to look at the functionality of hair," Ou told Live Science. In nature, hair has many structures and serves many purposes, such as for warmth, physical protection, sensation or movement.
After developing the new printing technique, Ou and his colleagues began experimenting with different applications of their own. They found that by controlling the orientation of hair they could give a pair of surfaces adhesive qualities, like Velcro. And by vibrating the hairs, the same qualities of tilt and direction could induce and control motion in objects placed on a printed surface.
Ou said designers could pattern a patch of fur to direct the movement of objects on the surface, and by varying the frequency from a vibration source, move only objects up to a certain weight. As a result, 3D-printed fur could be part of a system for automatically sorting small objects by weight, he added.
The researchers also created a model, in the form of a toy rabbit, for how the artificial hairs could be used as a sensory tool. When petted front to back, a microphone embedded in the rabbit picks up a signal and the rabbit lights up green. But when rubbed the "wrong" way, the fur sounds different, and the rabbit will flash red.
Sign up for the Live Science daily newsletter now
Get the world’s most fascinating discoveries delivered straight to your inbox.
The hair is made in stereolithography printers, which expose parts of a liquid volume of resin to ultraviolet (UV) light, hardening it into a finished product.
The MIT team had a second motivation; one shared by other researchers.
"We were mostly concerned with how to expand the types of objects you can print," said Gierad Laput, a graduate student in the Human-Computer Interaction Institute at Carnegie Mellon University in Pittsburgh, who was not involved with the MIT study. Laput led a team of researchers that developed a different technique for making 3D-printed hair using cheaper, more common machines that he compares to a glue gun. Laput and his colleagues presented their process in November 2015 at the ACM Symposium on User Interface Software & Technology
"Both [techniques] have advantages and disadvantages," Laput told Live Science. For example, he said their technique of using so-called fused deposition modeling can print more hair-like, longer strands that can be manipulated in different ways, like braiding. MIT's stereolithography, on the other hand, can print in much finer detail, enabling many of the researchers' proposed applications. "There's lots of good things to say about both projects, and I'm glad that research is moving forward on these fronts," Laput said.
But despite the differences between the techniques and the finished products, both Ou and Laput can agree on one thing:
"The major purpose of this process is not to print a wig," Ou said, "because if you want a wig, you can buy a wig."
"It's really impractical to print wigs with both techniques," Laput said. "They're not optimized for this. The wig-making industry is optimized for making wigs."
Original article on Live Science.