Powerful Ideas: Wind Turbine Blades Change Shape
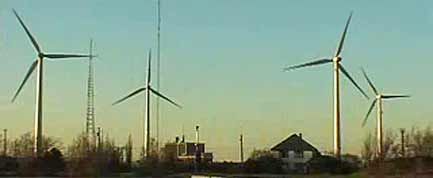
Morphing blades made of advanced composite materials that can rapidly change their shape depending on the wind could help lead to advanced wind turbines that perform better and last longer.
Wind energy is growing more and more popular worldwide. The United States is currently the world's largest generator of wind energy by total megawatts, and by 2030, the Department of Energy predicts that as much as one-fifth of the nation's power might come from wind. On a per capita basis, other nations are even further ahead of the United States — Denmark, for instance, already gets one-fifth of its power from the wind.
To help wind turbines advance further, scientists are looking into morphing blades, which can rapidly change their aerodynamic profile to best suit the prevailing wind conditions.
"The idea was born from a simple observation of a fish in an aquarium," said researcher Asfaw Beyene, a mechanical engineer at San Diego State University. "Many flying and swimming animals have superior efficiencies than manmade devices. The primary difference between natural motion and motion of manmade devices is lack of geometric adaptability to varying flow conditions.
"In flying and swimming creatures, the geometries morph to fit to a flow condition," Beyene added. "In man-made devices, typically the geometry remains rigid in spite of widely varying flow conditions."
Beyene is leading one team exploring morphing blades for wind turbines. Another team is working at the University of Bristol in England.
"The wind can be very harsh on blades — turbines turn off if the wind gets too much, or else the blades will break fighting the wind," explained researcher Paul Weaver, an aerospace engineer at the University of Bristol.
Sign up for the Live Science daily newsletter now
Get the world’s most fascinating discoveries delivered straight to your inbox.
"A morphing blade uses the wind to its advantage rather than fighting it, adapting its shape to get greater performance," Weaver added. "This has the potential to significantly relieve unwanted stresses in the blades, increasing their efficiency and helping to prolong their life."
Modern wind turbine blades are typically made from a combination of glass and carbon-fiber-reinforced plastics. During manufacture, the plastic resin is heated and cooled in a controlled manner so that it bonds with the fibers and sets to form a rigid structure.
By carefully controlling the direction and tension of the fibers, the researchers at the University of Bristol note it is also possible to create a composite that can snap between two distinct rigid shapes. For instance, when given an electric signal, the blade might flex one way instead of another, showing more or less of its surface to the wind.
Weaver noted that his team had achieved a working demonstration of a morphing helicopter rotor blade. He and his colleagues have now entered into an agreement with Denmark-based Vestas Wind Systems to develop composite materials for future products.
Beyene envisions morphine wind turbine blades made out of plastic materials similar to urethane rubber that flexibly bend and twist shape to reach the optimal angles that get as much energy from the wind as possible, depending on the wind's strength. He explained they have completed lab tests with a number of roughly 3-foot-wide (meter-wide) rotors made from a number of different materials.
"The results are very promising," Beyene said.