Corn Stalks Engineered to Self-Degrade into Fuel
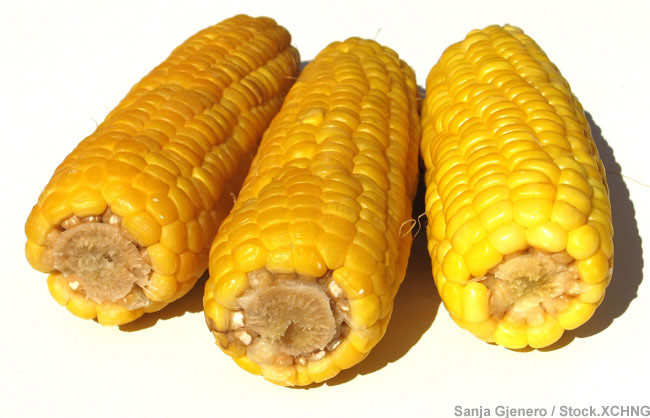
With gas prices tipping the $3-a-gallon mark, many are looking at other ways to fill the tank. Ethanol made from corn is one promising substitute. Another idea is to use the inedible parts of corn plants—called biomass.
"Converting biomass would add value to the corn residues that are currently not used," said genetic engineer Mariam Sticklen of Michigan State University.
But breaking down corn leaves and stalks into usable sugars is expensive. To help reduce costs, Sticklen and her colleagues have genetically tailored corn plants to manufacture the necessary enzymes in their own tissues.
This would streamline production and increase the harvest value for farmers. Sticklen's team were issued a patent for their corn in 2006, and currently three undisclosed companies have expressed an interest in licensing it, Sticklen told LiveScience.
Grain gain
While criticized by some scientists as not being energy efficient, ethanol is considered by many researchers to be an attractive alternative to gasoline.
And like other bio-fuels, ethanol would decrease energy dependence on unstable petroleum-rich nations.
Sign up for the Live Science daily newsletter now
Get the world’s most fascinating discoveries delivered straight to your inbox.
All cars can—and some already do—run on gasoline mixed with small amounts of ethanol (roughly 10 percent), In the U.S., almost all this ethanol comes from fermenting the simple sugars in corn grain.
However, despite being the country's largest food crop, "we have a limited amount of corn grain," Sticklen said.
Even if everyone went on maize-free diets and put every ear of corn into ethanol, it would meet only 15 percent of U.S. transportation fuel needs, Sticklen said.
Easy to digest
One way to increase output is to use other parts of the plant. Specifically, corn leaves and stalks contain cellulose, a tightly wound chain of sugars that provides plants their support.
To make ethanol, cellulose needs to be "digested" by a special type of enzyme called cellulase. In the last 5 years, the cost of making cellulase has dropped by a factor of 25, thanks to genetically engineered bacteria that act like tiny cellulase factories.
Still, cellulose-derived ethanol costs about $2.30 a gallon. To compete with other fuels, the price needs to come down to between $1.00 and $1.50, Sticklen said.
Sticklen's engineered corn could help by making its own cellulase and storing it in isolated regions. Fortunately for the plant, the enzymes would only start degrading cellulose when the plant is crushed up and heated.
If incorporated into ethanol production, this corn could save money and time because "it would be moving a processing step back into the agriculture stage," said Reid Detchon, executive director of Energy Future Coalition. But Detchon added that it might be some time before it finds use, as there are currently no large-scale cellulose-derived ethanol facilities.
Sticklen can control where the cellulase forms, so she can keep it out of the kernels we eat.
And to address concerns that modified genes might spread into nearby fields, she has been developing a corn in which the cellulase-producing gene does not show up in pollen grains and therefore could not be passed down through simple reproduction.
- What's Your Environmental Footprint?
- Top 10 Emerging Environmental Technologies
- Ethanol: Energy Panacea or False Promise?