Searching History for the Cement of Tomorrow
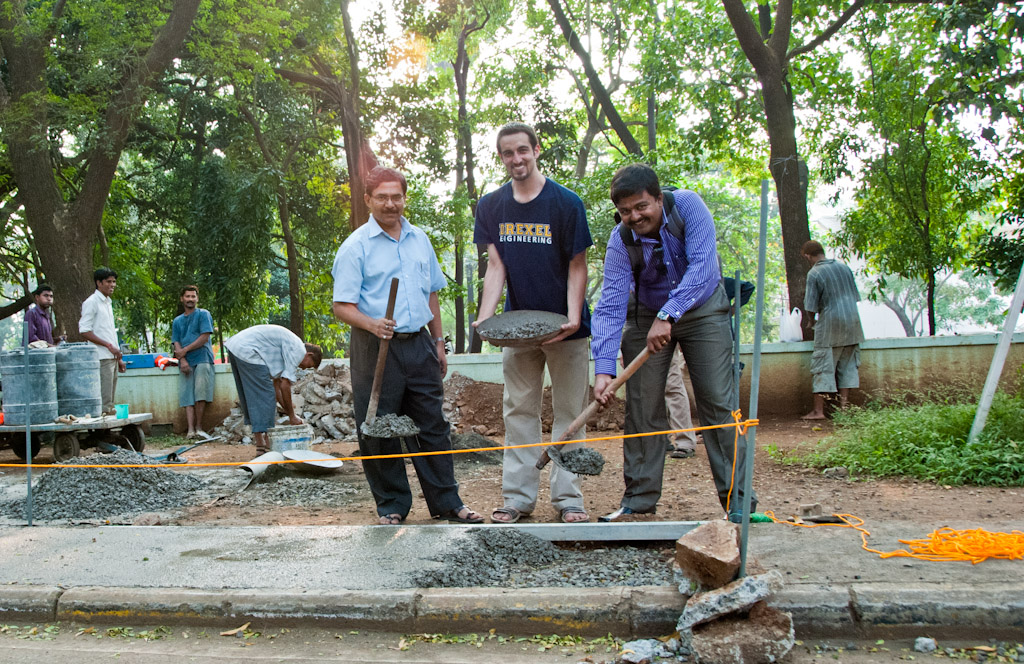
This Behind the Scenes article was provided to LiveScience in partnership with the National Science Foundation.
If you want to cook up some environmentally friendly cement, just mix two cups of granulated garden limestone, one cup of ground granulated blast furnace slag and three tablespoons of soda ash (i.e, sodium carbonate). What results is a strong, sustainable and economical alternative to ordinary Portland cement (OPC), the industry leader in cement. Researchers in Michel Barsoum’s group at Drexel University have been cooking up this seemingly new technology over the last several years, but its origins go back much farther than one may realize.
To the Great Pyramids of Egypt, in fact. Barsoum’s group had conducted research that seemed to prove some of the stones in the pyramids were cast using an early form of cement, rather than carved out of limestone. If some of the materials used to build the pyramids were indeed cast, and have lasted for 4,500 years, why not use them in today’s building materials, he wondered?
“OPC is responsible for 5 to 8 percent of the world’s COand consumes an enormous amount of energy,” says Alex Moseson, a colleague now taking the lead on bringing Barsoum’s alternative to market.
Greenstone cement ingredients
The difference between the Drexel-created “Greenstone” cement, as it is called, and ordinary Portland cement lies in the ingredients and methods used. Greenstone is an alkali-activated cement (AAC) that doesn’t require heating when made. Rather, the AAC relies on recycled ingredients that are readily available — mostly industry waste products that have already been heated. These include fly ash, chimney soot captured from coal-fired power plants and slag, which is a byproduct of the process that turns iron ore into iron.
As a result Greenstone’s environmental impact profile is dramatically different than OPC’s, showing 97 percent less energy consumed and also CO2 produced. Additionally, the ready availability of raw materials brings the cost of manufacture from $75 per ton to approximately $50 per ton. With anticipated carbon credits, Greenstone yields an additional $5-$20 per ton benefit.
Get the world’s most fascinating discoveries delivered straight to your inbox.
But how does it compare to OPC in performance? “Our results and the literature confirm that it performs as well or better than OPC,” says Barsoum. The group is close to seeing the cement pass industry tests that set benchmarks for strength, set time and volumetric stability.
As importantly, says Moseson, “We have always worked toward cement that works in the real world, not just the lab. That means shelf stability, workability, room-temperature curing, easy transport and more.”
Moseson pursued such real world application while at IIT Bombay in Mumbai, conducting research for his dissertation. He worked with local researchers to develop an AAC that met the standards set out in India for cement and investigated how Greenstone production might empower people living in slums. Today, three products made of local materials, using local tools and labor, are currently under consideration by a major cement manufacturer there.
The group has taken Greenstone and formed a company, Greenstone Technologies, Inc. They began publishing scientific results about their findings in 2009 and a November 2011 publication in Cement and Concrete Composites discussed the Drexel green cement’s practical potential. The researchers are currently talking with investors and possible partners. With the claim to benefits of reduced cost, reduced pollution and enhanced performance, are there obstacles to putting the Drexel cement out on the market? “The challenges for getting this out into the market include the variation among feedstocks ... and the time it takes to validate a new material,” says Moseson. “While our research allows us to compensate for variation, it would help if processors think of fly ash and slag [feedstock] as co-products instead of by-products to help standardize these materials for use in the cement.
“We also have to overcome powerful market forces. OPC is a $300 billion global market and convincing builders and industries to use something else is difficult. Convincing people that our cement will last as long as OPC when it is newer is also a challenge.” Additionally, their product is not patentable due to a great deal of prior art — or prior knowledge related to the technology — from as early as the 1950’s, which is sometimes a deterrent to investors. Despite these hurdles, interest in their work is increasing.
Interestingly, AAC is not totally brand new. In the 1950s and 1960s, a form of AAC was successfully used in some buildings in the former Soviet Union. In addition to the Great Pyramids of Egypt, much of the inspiration for this research came from ancient Rome. “Everything that the Romans built was made of similar ingredients,” says Moseson. “Although we won’t know for 2,000 years if ours have the longevity of Roman buildings, it gives us an idea of the staying power of this stuff.”
Editor's Note: The researchers depicted in Behind the Scenes articles have been supported by the National Science Foundation, the federal agency charged with funding basic research and education across all fields of science and engineering. Any opinions, findings, and conclusions or recommendations expressed in this material are those of the author and do not necessarily reflect the views of the National Science Foundation. See the Behind the Scenes Archive.