Shrinking the Carbon Footprint of a Widely Used Chemical
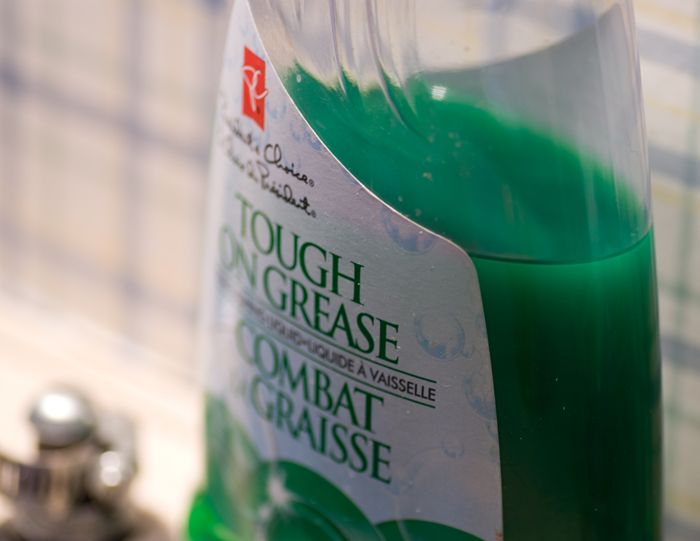
This Behind the Scenes article was provided to LiveScience in partnership with the National Science Foundation.
Nearly everyone alive on the planet has drunk from, sat on, worn, washed up with or driven in something made from ethylene oxide. That's because all sorts of household items are made from this essential building block, including plastic soda bottles, polyester fibers, detergents and anti-freeze. Ethylene oxide, or EO for short, has a huge market — a whopping $30-billion-per-year market — that shows no signs of subsiding.
Over the years, methods for manufacturing EO have improved significantly. Still, the current process for making EO puts out about 3.4 million metric tons of carbon dioxide each year, more than most other manufactured chemicals and roughly the same emissions caused by 900,000 cars annually.
In 2007, Daryle Busch of the University of Kansas (KU) Center for Environmentally Beneficial Catalysis (CEBC) joined forces with CEBC director Bala Subramaniam to design a greener ethylene oxide process, with help from postdoctoral researcher Hyun-Jin Lee and chemical engineering PhD graduate Madhav Ghanta. "We knew it wasn't going to be easy to eliminate the carbon dioxide byproduct," said Busch, a distinguished professor emeritus of chemistry at KU. "But it was an opportunity to make an enormous difference."
No burning
The research team is developing a revolutionary new way to make EO using hydrogen peroxide as the oxidant instead of the usual oxygen gas.
It's no surprise that mixing oxygen gas with highly flammable ethylene at high temperatures could lead to unwanted burning and even a risk of explosion. Yet, this is how EO is currently made.
Sign up for the Live Science daily newsletter now
Get the world’s most fascinating discoveries delivered straight to your inbox.
In contrast, the new CEBC technology dissolves ethylene in a liquid mixture of methanol, hydrogen peroxide and a catalyst at close to ambient temperatures. This method is more efficient. It completely eliminates the burning of ethylene and EO that typically occurs in the conventional process. No burning means no CO2 byproduct.
"Our new technology has the potential to save $2 billion worth of chemicals from going up in smoke each year," said Subramaniam.
The team also needed a catalyst that could help transfer an oxygen atom from hydrogen peroxide to ethylene. Surprisingly, they found that methyl trioxorhenium, which had been studied for years in other applications, could do the job. It works so well that more than 99 percent of ethylene molecules are converted to EO without decomposing hydrogen peroxide.
In 2010, the American Chemical Society Green Chemistry Institute recognized the novel ethylene oxide process by awarding Ghanta one of two Kenneth G. Hancock Memorial Student Awards.
How much does it cost?
The patented technology offers a cleaner alternative process for making an essential commodity chemical. But this greener approach must be more expensive, right? Not necessarily.
"We used state-of-the-art tools to estimate the cost of the new process and found that the economics are on par with the conventional process," said Subramaniam.
With funding from the National Science Foundation Accelerating Innovation Research program, Subramaniam's team now is searching for ways to further reduce the manufacturing costs of the new technology. They can cut costs by approximately 17 percent if they can overcome three barriers. First, they must demonstrate that they can selectively oxidize ethylene from a cheaper mixed ethylene/ethane feedstock. If so, they could save about 10 percent of costs by eliminating the need for purified ethylene. They also estimate 5 percent savings by improving peroxide efficiency and 2 percent savings by finding a cheaper, more durable catalyst.
"These advances will likely make our novel technology very attractive to chemical companies, especially those companies in the U.S. looking to utilize abundant natural gas feedstocks," said Subramaniam.
While the researchers originally targeted EO to shrink its super-sized carbon footprint, it looks as if their new technology could offer economic benefits as well.
Editor's Note: The researchers depicted in Behind the Scenes articles have been supported by the National Science Foundation, the federal agency charged with funding basic research and education across all fields of science and engineering. Any opinions, findings, and conclusions or recommendations expressed in this material are those of the author and do not necessarily reflect the views of the National Science Foundation. See the Behind the Scenes Archive.