Like A Rock: New Concrete Could Last A Lifetime
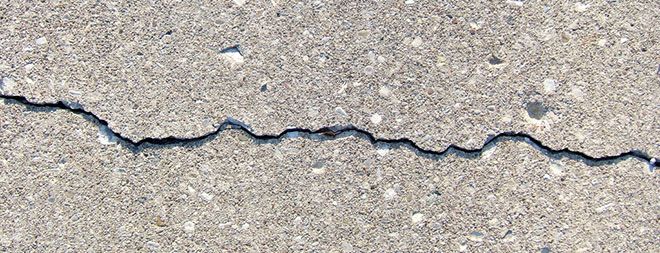
Updated Friday, April 18, at 4:25 p.m. ET.
(ISNS) – On the surface, concrete seems like one of the world’s most durable substances. After all, 2000-year-old Roman buildings made of the material are still standing. But with longevity comes problems: cracks in vital areas can make bridges and sidewalks impassable.
Scientists may be inching towards a solution for the future of concrete. Scott Muzenski, a graduate student in civil engineering at the University of Wisconsin-Milwaukee, was inspired by a crack in a parking structure near his office to delve into the science of what holds stuff together. Muzenski and his advisor had been tinkering with creating concrete with superhydrophobic qualities – stuff that shuns water – that also had the ability to be consistently monitored remotely.
“We have been getting a lot of good results in the lab, so we decided to put our findings into the concrete slab in the parking lot,” says Muzenski. The room-sized slab is now embedded with electrodes that monitor stresses to the concrete and can alert the researchers to any developing dangers.
The embedded sensors can measure resistance between electrodes, and by monitoring electrical changes, the researchers can tell whether a crack has occurred or whether corrosive chemicals or water is present. They could also collect information about loads and trucks traveling over the material. “The slab could text or email someone if there’s a problem,” says Muzenski. “Having that instantaneous response would be pretty important.”
According to the Federal Highway Administration, the average life of a concrete road is about 40 years, but that can be much lower in a place where freezing and thawing wreak havoc on the structure. Muzenski and his advisor Konstantin Sobolev say their durable, water-resistant and malleable paving material could last 120 years under normal conditions.
Other efforts to improve the world’s most common building material have focused on sealing off the top to prevent water and salts from seeping in. Muzenski took a different tack: he mixed water, oil and tiny particles into the concrete itself.
Sign up for the Live Science daily newsletter now
Get the world’s most fascinating discoveries delivered straight to your inbox.
Typically, concrete absorbs water. When the water expands during freezing, the concrete starts to crack. In addition, salts from salt trucks or rain water can corrode the steel that often reinforces the material.
The new material, dubbed a superhydrophobic engineered cementitious composite, is also more malleable than traditional concrete. That’s because the researchers added hair-sized fibers that bond with the concrete. When cracks appear, the fibers keep them from becoming bigger.
“This is the first time that the three components – hydrophobic materials, the ability to bend, and continuous monitoring - are put together at the same time,” said Francesca Tittarelli, a materials scientist at the Universita Politecnica delle Marche in Ancona, Italy. Tittarelli noted that each advance wasn't new unto itself, but they hadn’t previously been combined.
The ability to continuously monitor can reduce repairs on the roads, which are a headache for everyone.
“If we detect a problem as soon as it begins, that makes the intervention smaller and cheaper,” she said. “As in medicine, prevention is better than cure.”
Tittarelli added that in the future, concrete will have to clean up its carbon act. Producing a ton of cement, the main binding agent in concrete, also creates about a ton of carbon dioxide emissions. Her research team is looking for ways to make the process more sustainable. They’re also experimenting with geopolymers as binders for cement because they don't require heat.
Muzenski admits that the new technology isn’t great for every situation – some applications of concrete require more of a flow for construction, and the bendy fibers reduce the flow. In addition, the material would be too expensive to put everywhere that concrete is currently used. That’s why he said it can be targeted for critical infrastructure like bridge approach slabs (the link between bridges and the existing asphalt) and bridge decks.
When the snow started coming down in Wisconsin this fall, Muzenski had to pause the experiment with the slab, and he’s now looking forward to collecting the concrete’s data. “The slab itself that was out there was deteriorated and hadn’t been fixed in years, and we have a lot of damage due to freeze and thaw cycle,” he said. In addition to investigating better materials, “we thought we could do everyone a favor by replacing a part of the driveway outside.”
Editor's Note: This story has been corrected to identify one ton of cement, not concrete, as producing one ton of carbon dioxide emissions, and to indicate that researchers are experimenting with geopolymers as binders for cement, not concrete.
Inside Science News Service is supported by the American Institute of Physics. Katharine Gammon (@kategammon) is a freelance science writer based in Santa Monica, Calif., and writes for a wide range of magazines covering technology, society, and animal science.