Kitchen Recipe for Graphene Wonder Material Developed
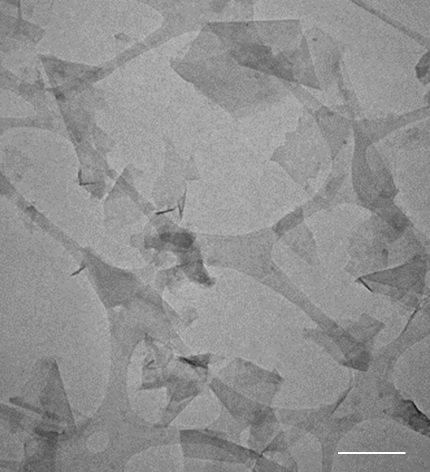
Graphene, single-atom-thick sheets of pure carbon, is lighter than steel but many times stronger, with better electrical conductivity than copper. It's even transparent. One day graphene could support flexible electronics, solid lubricants and even a space elevator.
But before that happens the stuff must be mass-produced, and a team led by Jonathan Coleman, a professor of chemical physics at Ireland's Trinity College in Dublin, thinks they've found a way to do it. They put graphite (from which graphene is derived) into a solution and stirred it with rotors moving at thousands of revolutions per minute — which worked even with an ordinary blender. Their work is detailed in the April 20 issue of the journal Nature Materials.
Making lots of graphene isn't easy. There are a number of methods, such as chemical vapor deposition, which involves turning carbon into a vapor that collects on a surface, heating silicon carbide (SiC) to leave the pure carbon — graphene — behind, or simply tearing off sheets of single carbon atoms from blocks of graphite. The latter method is called the "Scotch Tape" method, because initially tape was stuck to a graphite block and the graphite was just peeled off. [8 Chemical Elements You've Never Heard Of]
Current methods, though, are expensive and difficult to carry out on an industrial scale. On top of that, to get the wonder-material properties, graphene has to be of high quality — the carbon atoms that form the sheets have to be in near-perfect hexagonal patterns.
Making graphene
Coleman said his team started from methods involving bombarding graphene in liquid form with high-frequency sound. They wanted to make the material without the ultrasound, simplify the process and cut energy costs. When they tried stirring the liquid, they produced high-quality flakes of graphene.
"Under the electron microscope it looks just like a diagram in a textbook," Coleman said.
Sign up for the Live Science daily newsletter now
Get the world’s most fascinating discoveries delivered straight to your inbox.
The stirring works in two ways. First, the liquid is spinning around and it's not moving at the same speed throughout. So the grains of graphite get hit with more force on one side than the other, a phenomenon called shear. Carbon atoms in graphite are arranged in hexagonal patterns like chicken wire, piled on top of each other in layers. The bonds between the layers are weaker than the bonds within them, so when the buffeting in the water breaks up the grains, they tend to break into flat sheets — graphene.
Ordinarily the sheets of graphene would stick back together in clumps. But that's where the solvent comes in. One of the solvents they used was N-methyl-2-pyrrolidone, common to the petrochemical industry. As the sheets of graphene separate the solvent sticks to the carbon atoms. That keeps the single sheets of graphene separate, with the result being a liquid solution full of micrometer-size flakes of pure, high-quality graphene.
What's next for kitchen-made graphene
Though the sheets are tiny, this process can make lots of them. And unlike other processes for making graphene, if some of the carbon doesn't make the perfect sheets that's OK, because the non-graphene carbon can be filtered out and put through the process again.
Besides chemical solvents the process also works with surfactants in water. The team even tested a kitchen blender using ordinary dishwashing liquid.
The researchers made up to 21 grams (about seven-tenths of an ounce) of graphene using 300 liters (80 gallons) of water and surfactant. That may not sound like much, but it's enough to cover about 290 square feet. Coleman said he and his team are working with a British company, Thomas Swan, exploring how to commercialize this production method.
Other research teams are looking at other methods. A start-up in Philadelphia, Pa., Graphene Frontiers, got a $744,600 grant from the National Science Foundation to explore chemical vapor deposition, what it calls a "roll-to-roll" process.
And there are still challenges to making the equipment used in Coleman's study: A small rotor in a blender or laboratory table is not moving as fast as a large one in an industrial vat. But the fact that even a blender works bodes well for future manufacturing — it means the equipment should be relatively simple. Coleman noted there was some surprise that a blender could generate enough energy.
Follow us @livescience, Facebook & Google+. Original article on Live Science.