
Virus-Crafted Metal Nano-Sponges Boost Boiling
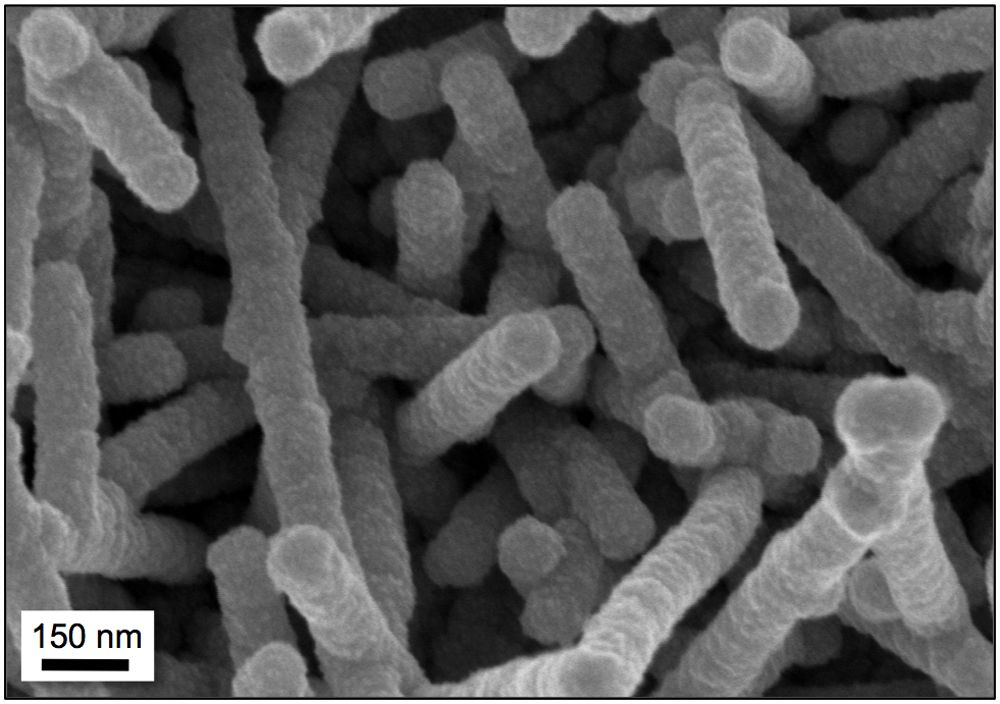
Britt Faulstick, engineering and technology news officer at Drexel University, contributed this article to Live Science's Expert Voices: Op-Ed & Insights.
Three shelves full of leafy, green, tobacco plants take their place under the growing lights next to the microscopes, fume hoods and heat-transfer experiments in Matthew McCarthy's lab.
Unlike most tobacco farmers, McCarthy isn't worried about the health of his crops — in fact, he's actually taking steps to ensure they get sick. McCarthy grows the tobacco to harvest the plants' viruses, tiny nanomachines that are perfect templates for rapidly manufacturing nanostructured coatings. [Nanoscale Super-Sponges Boost Boiling (Gallery )]
"Mosaic viruses" as machines
Admittedly, as a mechanical engineering professor in Drexel University's College of Engineering, McCarthy isn't much of a green thumb, but just a few dozen plants will yield trillions of tobacco mosaic viruses — and that's what he's really after. McCarthy's talent lies in using the minuscule protein bundles to engineer nanostructures that can change the properties of the surfaces to which they're attached.
Tobacco mosaic virus was one of the first viruses, of any kind, to be identified and widely studied, due in some part to the devastation they caused at the turn of the last century. In McCarthy's Microscale Thermofluidics Laboratory, the viruses have found a more beneficial niche as self-assembling scaffolding for nano-construction.
McCarthy and his doctoral assistant Md Mahamudur Rahman have engineered viruses to cling to a variety of surfaces — from stainless steel to gold, and just about every combination in between. They approached the U.S. National Science Foundation with a proposal to make these surfaces better at boiling water, and with the funding are now producing structures that do exactly that.
Sign up for the Live Science daily newsletter now
Get the world’s most fascinating discoveries delivered straight to your inbox.
It's not just as easy as boiling water
Phase-change heat transfer, the technical moniker for boiling water, is ubiquitous in nearly all industries. It plays a critical role in electrical power generation, chemical processing, water purification and HVAC systems in residential and commercial buildings — to name just a few applications. So even modest improvements to the phase-change heat transfer process could translate to energy and cost savings on a large scale.
If McCarthy’s work is one day put to use in steam-producing power plants, it has the potential to improve not only their efficiency, but also the maximum temperature at which they can safely operate — thus enabling them to produce more energy. [Steam Machine Turns Poop into Clean Drinking Water ]
Enhanced boiling delays the onset of the undesirable condition engineers call critical heat flux (CHF). This is essentially the failure of a surface during boiling. When CHF occurs, the production of vapor cannot be balanced by replenishing liquid, and that is the first step in a dangerous progression that can cause the destruction of electronic components or even the catastrophic meltdown of a nuclear reactor.
"One route to enhance the way a surface transfers heat during boiling is to control how hydrophilic it is," Rahman said. Hydrophilic surfaces are particularly effective at attracting water. "A surface can produce steam at a higher rate if it's able to quickly rewet itself during boiling. This allows rapid boiling to safely occur at higher heat fluxes."
Drawing water toward the heat
The science behind McCarthy's work is the same that drives the design of high-performance athletic apparel and thermal gear: capillary action. To keep the wearer dry, microfiber material wicks perspiration away from the body by drawing it into the tiny spaces between its woven fibers. Using the viruses, McCarthy creates a coating of porous metallic structures that draw water down into the spaces between them, which keeps the water molecules in contact with the boiling surface.
"This is time-tested science, it's the same reason a paint brush draws in paint or a dry sponge absorbs water." McCarthy said. "We've just figured out how to turn a piece of metal or a composite material into something more sponge-like using an extremely thin surface coating."
The researchers built each virus with a chemical binding site at the tip of its protein chain. This allows the viruses to attach to just about any metallic surface they contact. Each virus has a slight electrostatic charge, so while it's binding to a surface it's also pushing itself away from surrounding viruses, which is how the structures are able to arrange themselves in relatively vertical positions. This alignment is important because it creates a space, between the tip of each virus structure and the boiling surface, into which water can be drawn.
Building virus sheets
Viral biotemplating is the process of using viruses as a scaffold for making nanostructures. It's a tool McCarthy learned to use as a post-doctoral researcher at the University of Maryland, where he worked with Reza Ghodssi and James Culver to use tobacco mosaic viruses for enhancing micro-battery performance.
Using similar techniques, McCarthy's lab can coat full surfaces simply by submerging them in a viral solution for 12 to 24 hours, letting the grass-like substrate take root. Then, the researchers coat the viruses with palladium and nickel to form the actual nanostructure that will do the wicking. The entire process can be completed at room temperature in a little over a day, which makes it quick and easy to repeat on a variety of surfaces.
"As mechanical engineers studying fluidics, it's very helpful to have a number of different samples to study," McCarthy said. "We can better understand the nature of phase-change heat transfer by observing and comparing the behavior across surfaces of different composition and shape."
In addition to coating different metallic surfaces with the virus-templated nanostructures, the group is designing surfaces with particular shapes that could help control the formation of vapor bubbles during boiling.
"Right now we're specifically studying the fundamentals of boiling heat transfer and its enhancement, but this technology could one day be applied to new heat exchanger designs and high-performance thermal management systems of the future," McCarthy said. "It could also be used to retrofit existing heat exchange systems with self-assembled viral nanostructures — which could prove to be a cost-effective way to improve their efficiency."
As McCarthy’s research moves forward, the team will identify the best combination of surface design, materials and nanostructure coating to produce the most efficient heat transfer. Preliminary results are already quite promising. The super-wicking surfaces have shown a tripling in the efficiency of the boiling process and a 240-percent increase in the maximum heat-transfer rate at which critical heat flux occurs.
Follow all of the Expert Voices issues and debates — and become part of the discussion — on Facebook, Twitter and Google+. The views expressed are those of the author and do not necessarily reflect the views of the publisher. This version of the article was originally published on Live Science.