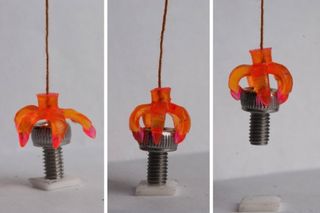
Bendable 3D-printed structures that, when heated, quickly snap back to their original shapes could help make sophisticated drug-delivery devices or origami robots, researchers said.
Engineers from the Massachusetts Institute of Technology (MIT) and Singapore University of Technology and Design have devised a new fabrication process that uses ultraviolet (UV) light to print successive layers of polymers into 3D, Transformer-like structures that "remember" their shapes.
The creators call the process 4D printing, because the structures change over the fourth dimension — time — when subjected to a stimuli like heat. This is the first time 4D printing has been done on the submicrometer scale and with response times measured in tens of seconds rather than tens of minutes, the researchers said. [The 6 Strangest Robots Ever Created]
To demonstrate the power of the technique, the team printed a rubbery, claw-like gripper that could grasp and lift an object when heated. The researchers were able to use multiple materials and design actuators — components responsible for moving devices — at the scale of a human hair. This accomplishment means the technique could eventually allow the team to 3D print sophisticated, foldable, soft robots, the researchers said.
"Enabling all the different folding mechanisms in one structure would really require a complex geometry and also proper design of the actuation components, which is why I think this is really enabling technology and there is a lot of room for new innovation," study co-author Nicholas Fang, a mechanical engineer at MIT, told Live Science.
Printing bendable structures
The printed objects ranged from flowers to a 1-inch-tall (2.54 centimeters) replica of the Eiffel Tower. The structures could be stretched, twisted and bent at extreme angles before springing back to their original shapes within seconds of being heated. The researchers described the bendy polymers in a paper published in August in the journal Scientific Reports.
The rapid reaction times are a direct consequence of being able to print in smaller dimensions, because the higher surface-area-to-volume ratio transfers heat better, Fang said.
Sign up for the Live Science daily newsletter now
Get the world’s most fascinating discoveries delivered straight to your inbox.
"We are sure that we can speed up the actuation even further," he added. "The next thing for robotics applications is to show how much force this is able to provide."
Aside from miniature robots, the researchers said the approach could create actuators that help solar panels track the sun as its rays heat the panels. The new structures' ability to change shape without extra moving parts could also enable the creation of systems for deploying antennae on satellites, and these systems would be much lighter than mechanical ones, the engineers said.
The temperature-driven response of the structures could also be used in drug-delivery capsules that open upon early signs of infection, such as a fever, the researchers said.
"A drug-release device is a very good example of an application for such a material, because body temperature is very often a trigger or indicator of some physiological or pathological event," Fang said.
Miniature robots
To create the miniature structures, Fang and colleagues first constructed a 3D model using computer-aided design (CAD) software. This 3D design was then divided into hundreds of slices, and the pattern from each slice was projected onto liquid resins that solidify when exposed to UV light, just like the material dentists use to fill cavities.
To control these patterns at the micro-scale, the team borrowed high-resolution lens technology from the semiconductor industry. By modifying the properties of the resin or by using different combinations of polymers, the researchers were also able to adjust both the stiffness of the material and the temperature at which the structure's memory is activated.
Fang's team has also created other materials that respond to pH rather than temperature. In the future, it should be possible to construct devices activated by other stimuli, such as concentrations of DNA, salts or organic solvents in the environment, Fang said. "You can program these polymers and make them responsive to different triggers," he said.
The materials survived roughly 100 cycles of bending and heating, says Fang [this wasn’t reported in the study, he just said it so feel needs emphasis immediately after] but the team now plans to properly test the effects of fatigue on the polymers. The researchers also plan to develop even finer control of the printing process, and could be printing at scales 20 times smaller than they are currently within a year, he said.
Original article on Live Science.