Future Computer Chips Could Assemble Themselves
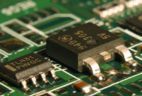
The reason computers have relentlessly advanced in power over the years is because circuitry has grown ever smaller over time, allowing Intel and others to pack more onto microchips. However, these features are now getting so small that soon the process that has been used to make them for the last 50 years will no longer work.
Currently, microchips are built up, layer by layer, through a process called photolithography. A layer of silicon, metal, or some other material that will make up the circuitry is deposited on a chip and coated with a light-sensitive material called a photoresist.
Light shining through a kind of stencil — a "mask" — projects a detailed pattern onto the photoresist, which hardens where it is exposed. The unhardened photoresist is washed away, and chemicals etch away the bare material underneath.
A physical barrier
The problem now is that chip features are significantly smaller than the wavelength of the visible light used to make them. The microchip industry has developed a number of tricks to get light to generate patterns smaller than its own wavelength, but these will no longer work as scales get below roughly 40 nanometers. For comparison, a human hair is about 100,000 nanometers wide.
One possible way to continue shrinking chip features would be to build electronics from the bottom up with components that are already small, instead of trying to etch tiny features into relatively large chunks of matter from the top down.
The problem, however, is that the molecules that will assemble into these circuits need some kind of template to line up on, and making such templates can be relatively cumbersome.
Sign up for the Live Science daily newsletter now
Get the world’s most fascinating discoveries delivered straight to your inbox.
For instance, electron beams can generate trenches in microchips. These channels are much smaller than ones that light can produce because electrons are infinitesimally smaller than wavelengths of light. However, while light can shine through a mask and expose an entire chip at once, an electron beam has to move back and forth across the surface of a chip, much like a typewriter printing line after line of text. This makes so-called electron-beam lithography slower and significantly less efficient and more expensive than conventional optical lithography.
A new production method
Now researchers at MIT have taken a critical step toward making self-assembling systems far more practical. The key is using electron-beam lithography far more sparingly.
Instead of creating lines with electron beams, researchers used them just to make stubby pillars of silica glass just 35 nanometers high and 10 nanometers wide on a silicon chip.
The chip is covered with a material that upon contact with the electron beam transforms into glass, and the rest of the material is washed away. Such rows of dots could be made in one-thirtieth or even one-hundredth less time than solid lines would require, the researchers explained.
These columns serve as hitching posts for polymers – long chains of similar molecules – the researchers deposit onto the microchip. These polymers can then spontaneously arrange themselves into patterns useful in circuit design, such as stripes 17 nanometers wide, as well as zigzags, curves and junctions.
These arrays can then be modified with electrically charged gas to serve the same purpose that hardened photoresists do in photolithography — protecting the material beneath them while is the rest of the material is etched away to help produce circuits.
It's a bit like 'connect the dots,' explained researcher Caroline Ross, a materials scientist at MIT.
"We have to put just enough dots so the polymer knows where to go next. It's a combination of top-down, with the electron beams, and bottom-up, with the self-assembly."
Like oil and water
The microchips of the future could help assemble themselves using a newly developed technique that could allow molecules to arrange themselves into tiny circuits, scientists say.
The researchers used two different kinds of polymers — polystyrene, found in Styrofoam and often in plastic cups, and PDMS, a kind of silicone rubber.
"These two chains don't like to mix, but we're forcing them to be together," Ross said. Like oil and water, "they would like to separate, but they can't, because they're bonded together."
In their attempts to separate, the different types of polymer chains arrange themselves into predictable patterns. By varying the length of the chains, the proportions of the two polymers, and the shape and location of the hitching posts, the scientists were able to produce a wide range of patterns.
The researchers are now working to find arrangements of their posts that will produce functioning circuits in prototype chips. They are also trying to refine their technique to produce even smaller chip features. In principle, one might use such techniques to go down to features 5 or 6 nanometers wide, Ross said.
She added that hard disk makers such as Seagate and Hitachi are interested in pursuing such methods, "so there's a real possibility this could show up in manufacturing in the next few years."
Ross, MIT electrical engineer Karl Berggren and their colleagues detailed their findings online March 14 in the journal Nature Nanotechnology.